Published on the 14/09/2008 | Written by Newsdesk
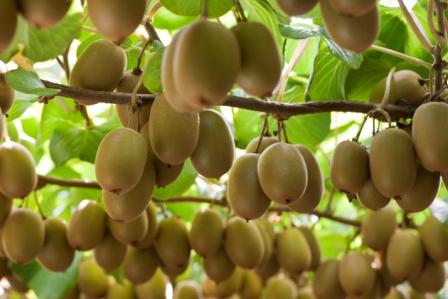
A growing number of businesses are realising the productivity, efficiency and accuracy benefits to be made by technology to fully integrate their supply chains. But what’s holding others back?..
Integrate an organisation’s supply chain by deploying barcode scanning – or even RFID technology – and you open the door to an exciting range efficiency benefits.
Scanners and barcoding technology are now relatively cheap. Even RFID tag prices have dropped significantly in recent years. So in theory it’s easy to implement a scanning system that achieves the fundamental goal of supply chain automation: removing the need to key in data related to product movements at multiple points along the supply chain journey.
Businesses are beginning to embrace the potential of the technology. New Zealand’s first major commercial roll-out of RFID utilising the Electronic Product Code (EPC) standard is well underway within the kiwifruit industry.
Standards organisation GS1 New Zealand, in collaboration with The Peacock Group, has designed – and given close ongoing support to – the implementation of a system that will enable kiwifruit processor EastPack to track and trace every pallet of the fruit it handles throughout its extensive Bay of Plenty operations.
Gary Hartley, GS1 NZ’s general manager sector development says this is likely to be the first substantial application of EPC/RFID in the Asia-Pacific region.
“It is certainly an application designed and implemented specifically to meet the demands of a large-scale operation in the heart of New Zealand’s export sector.”
EastPack’s quality focus
Each year, EastPack sorts, packs, stores and forwards to export a significant share of the nation’s $1 billion-plus kiwifruit crop. The company must respond constantly to international market signals received through the industry’s exporting arm, Zespri. It is a supply chain with major logistical challenges that reflect the competitive market positioning of New Zealand kiwifruit, a critical focus on product quality, and the scale and structure of this industry.
Hartley says in early 2007, EastPack turned to GS1 New Zealand for an innovative solution to the challenges posed by growth in the operation of its 42 cool stores. Its Te Puke site is the biggest such facility in the industry, handling 8 million trays during 2006-07.
“Pack house operation involves fruit going into cool storage, sometimes for months on end, then being retrieved to meet the requirements of particular orders, sometimes only hours before it is due on board a ship at Tauranga. Industry insiders say the height-of-season logistics of tracking and retrieving particular pallets in tightlypacked cool stores are nightmarish.”
The GS1 NZ recommendation built on EastPack’s experience with GS1-standard serial shipping container codes (SSCCs) and pallet bar coding, and on its existing inventory management system. In broad terms, the solution is simple: place EPC/RFID tags on pallets and RFID readers on forklifts; capture data electronically whenever a forklift picks up or drops off a pallet; identify where in the store these activities are occurring; and instantly transmit the data back to the inventory management system.
The Peacock Group and other technology suppliers were selected and a project team assembled to move quickly forward with test applications of the solution. These led to a fully-operational pilot with forklifts at one site operated in the business-as-usual rush to meet export orders.
Locations around the store were tracked through the use of forklift-mounted cameras and special data matrix bar codes attached to the ceiling: the cameras calculated the location through the bar codes directly above them each time a pallet was picked up or dropped off; the location was matched to cool store coordinates (row and position) fixed on a floor grid pattern; and this data, along with the SSCC of the relevant pallet and a time-stamp, was transmitted back to the management system in real time.
“The pilot results were impressive,” says Hartley.
“The accuracy rate for data capture in the management system exceeded 95% and the ceiling-mounted bar codes enabled pallets to be identified to within 20cm of their exact locations. From there, EastPack and its project team began a full-scale roll out of EPC/RFID at all 42 sites.”
EastPack, with close support from GS1 and its suppliers, have now implemented the solution across the company’s operation. The “go live” occurred in March/April, coinciding with the start of the 2008 export season.
“The value of the solution lives, of course, in EastPack’s vastly improved ability to locate particular pallets in store and to quickly retrieve them for export at optimum times and with minimum reshuffling of other pallets,” says Hartley.
“The management system already holds data on all fruit received for packing (eg. type, grower, harvest date) – and the system will now also hold real-time information on the location and status of that fruit by pallet SSCC.”
Based on this, the future benefits foreseen by EastPack are substantial.
EPC/RFID is expected to give EastPack a powerful tool for streamlining every aspect of its cool store operations. The system is designed to provide new streams of data on forklift movements, coolstore utilization and other variables on which to measure and improve the operating performance of each facility. This will open the way for savings in energy consumption, labour and time.
“It is early days and there are teething issues to be sorted out. This is after all, the first major roll-out of such technology in any industry in our part of the world,” says Hartley.
He adds that all parties expect the EPC/RFID solution will lead, ultimately, to reduced fruit loss, increased sales, cost savings and the avoidance of any missed-shipment penalties.
“Even with conservative assumptions, EastPack anticipates recovery of the capital costs during the first two years of implementation. The EastPack solution will mean ZESPRI receiving 15 percent of its product with EPC/RFID tags attached – and opportunities then open for wider application in the New Zealand kiwifruit supply chain, from grower to the supermarkets of New York, Paris and Tokyo,” he says.
“The implementation provides a valuable reference model for others outside of the kiwifruit industry to consider and potentially emulate. This is an extremely important step in the takeup of a technology likely to revolutionise supply chain management and logistics across many industries in the years and decades ahead.”
Overcoming cost and complexity
Supply chain automation and integration clearly has its attractions, so what is holding back other organisations that are yet to embrace it? The cost and complexity of changing existing systems remains a major barrier, says Maria Palazzolo, chief executive of GS1 NZ’s sister body across the Tasman, GS1 Australia.
“It’s very easy to say: ‘Look at your supply chain and look at where you can build efficiencies.’ That’s the easy side of it,” says Palazzolo. “The more complex side is that once you’ve identified those efficiencies you have to change processes and, in many cases, change practices that have been in place for many, many years.
Then normally there’s a whole IT factor that has to be considered as part of it, because IT is supporting the current processes and the current way the business is operating.”
Changing those systems is obviously a complex and costly process – the sort of project an organisation might take 10 years to fully complete.
Palazzolo says in that context, implementing changes to the supply chain is often something organisations brush aside to “look at doing properly” as part of that grand 10-year system upgrade.
GS1’s recommendation is that instead of putting supply chain integration in the too-hard basket, businesses look at deploying a few “easy wins” – introducing some scan-based automation that will result in improving efficiencies – as the first step towards embracing the potential of a fully integrated, global standards-based supply chain.
A regularly-heard excuse is that supply chain integration is not high on the list of corporate priorities, says Palazzolo.
“There are always very well documented, well justified reasons why companies don’t do as much as they could potentially do in looking at streamlining their supply chains and becoming a lot more efficient in taking out completely unnecessary and duplicated efforts which don’t have to be there, which ultimately add up to an inefficient supply chain.”
Palazzolo admits the majority of businesses join the organisation for reactive reasons: they’re asked to put barcodes on the products they sell by a customer, typically a large retailer.
“At that point we encourage them, quite aggressively, to look at the benefits they could derive by doing this for themselves – don’t just look at it as a cost of complying to what your customer wants, have a look at it as an opportunity to have a look at how your supply chain operates and how you can benefit from the things you’re going to have to do anyway for your customer – why not get the benefits out of it for yourself,” she says.
Palazzolo says a key issue affecting the uptake of RFID is that while in markets like the US, where powerful retailers such as Wal-Mart have mandated its use by their suppliers, that is not the case in New Zealand or Australia.
“[Here] we don’t have any retailers saying you must put an RFID tag on the pallet or on the carton [of products you supply]. Until such mandates happen in this country – if indeed they do – we will have companies who may want to take the initiative and implement it within their organisation, for their own benefit.”
Palazzolo says experience to date suggests the cost factor associated with changing technology will hold up RFID adoption, particularly because the massive amount of data RFID is capable of gathering means organisations embracing it need systems in place to process that additional data.
Michael Panosh, marketing manager for ERP vendor Pronto Software, put it this way in a recent paper: “Right now, the adoption of RFID across the retail supply chain is pretty much a Mexican standoff between manufacturers and retailers, with distributors stuck in the middle. Retailers see that RFID can help manage shrinkage and warranty processing overheads in their stores. For distributors, RFID will streamline handling procedures and improve supply chain visibility, lowering costs and improving operational efficiency. But for the manufacturers, RFID adds cost and complexity to products that are already operating on razor thin profit margins, though there is the glimmer of hope that RFID can deliver similar benefits to those offered to distributors.”
So, Panosh says, while it is obvious there is much to be gained from RFID, there are some fundamental issues that need to be overcome before the benefits be realised.
One issue, he says, is that everyone along the chain wants everyone else to pay for the infrastructure before they will adopt it.
Another issue, he says, is the lack of standardised technical specifications, incompatibility with business software and complicated implementation procedures. GS1, however, reject this claim, saying standards for RFID have become well established over the past couple of years.
And yet another issue Panosh raises is that while today’s RFID technology is suitable for pallet and carton tagging and tracking, it is not yet suitable for item level management. This means that while RFID can be useful in a warehouse environment, it does not yet readily transform retail operations.
Easy wins
Regardless of where RFID is heading, and how quickly, there is a risk that fixating on it can be a distraction to organisations looking for ways to utilise technology to boost supply chain efficiencies.
As Palazzolo points out, the answer is not to sweat the big stuff, but to look for the easy wins – the cost-effective ways to automate current human-error-prone procedures – and gradually integrate them into your other business systems.
RFID AT WORK Some examples of how New Zealand organisations are using the technology….Keeping tabs on bags Landed in Sydney but your bags are holidaying in Bangkok? You’re not on your own; the latest figures say over 42 million pieces of baggage went astray in 2007 and to add insult to injury, it is now taking 15 percent longer to return the bags compared to 2005. SITA, the IT provider which tracks passenger baggage worldwide for the air transport industry, released results from its WorldTracer system for tracing lost and mishandled passenger baggage used by 400 airlines and ground handling companies, showing 42.4 million bags were mishandled or delayed in 2007. In total the air transport industry handles around 2.25 billion pieces of checked baggage every year. Patrick Teo, CEO of New Zealand-based BCS Group, a major player in the airports and logistics sector with worldwide sales of its baggage and freight tracking and handling systems, says there is an industry-wide push to improvement both from a cost perspective to airports and to passenger satisfaction. “At BCS we are working on fine-tuning a fully integrated RFID based baggage management system that can track, trace and route passenger baggage from check in through to destination. We also have developed smart technology that provides an alert if baggage is tampered with during handling.” Teo says BCS ‘Virtual Airport’ software is helping airport management make more informed decisions as to peak flows and associated staffing, before issues occur. “We are seeing more pressures being put on airports in terms of security as well as bigger passenger volumes and faster turnarounds due to the new wide bodied aircraft such as the A380 and that can have a fl ow-on eff ect on baggage handling accuracy.” Iron-clad timing technology Organisers of the gruelling Taumaranui RSA Kururau Krusher turned to Times-7 Sport for the latest in active sports timing technology, which they say performed without a hitch. The new multi-sport tag has continued to excel at high profile events timed by Times-7 Sport including the Auckland Half-Ironman, Taupo Half-Ironman and the NZ Secondary Schools Individual & Team Triathlon Championships. Starting at Maraetai and racing past some of the most scenic beaches south east of Auckland, the Auckland Half-Ironman, now in its 5th year, utilised electronic timing for the first time this April. Race director Matthew Tuck, said he was very impressed with the IPICO Sports system that Times-7 Sport provided. “The results were available in split times and by category progressively throughout the race,” Tuck says. “Times-7 Sport gave us confidence that electronic timing is accurate and affordable, providing a better experience for the competitors”. Keeping shoplifters at bay Retailer Association chief executive John Albertson told the Howick and Pakuranga Times that supermarket chains were introducing electronic tagging for goods deemed “hot” for shoplifting. Such goods were usually small and expensive, and Mr Albertson said that over the next 18 months some would be secretly tagged, so they triggered exit alarms without giving any clues to would-be thieves. National retail theft losses amount to $650 million a year, or $1.8m a day, he said. As supermarkets accounted for about 20 percent of the retail spend, they carried a large share of the losses. Progressive Enterprises has a tagging programme for its 150 supermarkets in the Woolworths and Countdown chains, national security manager Ian Seed told the Dominion Post. |