Published on the 12/09/2017 | Written by Cincom
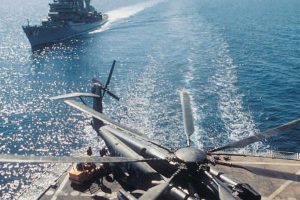
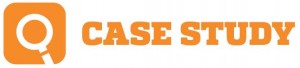
AT A GLANCE
INDUSTRY
- Engineering and Manufacturing
BUSINESS OBJECTIVE
- Take ERP in-house to reduce costs, improve security, and extend ERP benefits
- Coordinate front- and back-office operations
- Support a model of continuous business development
- Improve access to information from around the organisation
SOLUTION
- Cincom CONTROL and CONTROL Financials
BUSINESS BENEFITS
- Full implementation and training in nine months
- Improved decision-making and reporting capabilities
- Streamlined financial operations
- Better communication across departments
- New capabilities to address future opportunities
FOR MORE INFORMATION
Cincom
W:www.cincom.com.au
E: info@cincom.com.au
Graeme King – Country Manager
T: +61 2 8875 1400
Cincom raises the bar on flexibility, integration, and future functionality at Thales Underwater Systems…
Faced with an ageing ERP solution which was putting its compliance with applicable regulations at risk, Thales Underwater Systems turned to Cincom for an improved system. Thanks to the implementation of Cincom CONTROL, it has benefited from security enhancement by taking the system in-house, the elimination of siloed information in disparate business systems and made information and analysis readily available.
Thales Underwater Systems (TUS) was created in 1996 with the merging of Thomson Sintra Pacific and the sonar activities of GEC-Marconi. With a turnover of more than AUD$110 million, the Sydney-based engineering and manufacturing company employs more than 500 people in designing and manufacturing underwater sonar equipment for defence and civilian applications including offshore oil exploration.
Situation
TUS sought to bring its ERP in-house and sought full functionality, said Peter Quinlan, Operations Director. “The outsourced ERP wasn’t compliant and we felt improvements to that system would be excessively costly and a poor investment as the system had other limitations.”
Moreover, TUS needed to blend its back-office activities with those in the rest of the organisation. Linkage among various TUS units would give its financial staff a better picture of the organisation’s overall performance and to produce more meaningful reports.
Beyond these strategic motives, TUS wanted to reduce the cost of ownership, improve security and extend the ERP benefits.
On the financials side of the business, Management Accountant Troy Vegvari had known the difficulties in preparing reports with outdated information. Plus, “We wanted something that would enable us to continue doing our current activities, while at the same time allowing for future uses. And we wanted something that would give us an easy path to information from around the organisation.” He added that extracting information from the previous system was cumbersome and required considerable IT administration.
Solution
Cincom approached TUS at a time when, said Quinlan, the company was a highly educated, sceptical customers. “Ours is not a conventional manufacturing operation. We produce highly complex products and approach each as a mini-project. We might work on up to 100 projects, of varying scale, at any one time and these are spread between five separate business lines. To some extent, these business lines operate as sub-businesses, with their own personnel, resources and budgets.”
TUS identified four main reasons to change the ERP system and bring it in-house:
- A more cost-effective solution that ended its dependence on an outside service
- Security enhancement by taking the system in-house
- An end to information islands in disparate business systems
- More accessible and timely analysis of information
Rapid implementation was imperative; strategically, the company sought increased capability to support new initiatives and continuous improvement of its business processes.
Engineering change control was another concern.
“Our customers expect us to improve our products continuously,” explained Quinlan. “We must get maximum performance out of high-tech products and that can mean frequent change, often on a large scale.”
The new ERP system had to be flexible enough to support the culture of change that arises from constantly looking for ways to improve products. This meant coping with unusually deep bills of materials and with complex tracking of serial numbers of the numerous components within products – two capabilities offered by Cincom CONTROL.
Finally, “We do a monthly close, with our reports output by the fourth working day, with the next two days for management reports,” said Vegvari. “Previously most of this time would be spent compiling the reports.”
Giving the Cincom representatives one hour to acquit themselves, Quinlan was impressed by the company’s obvious understanding of his business needs and its experience in handling complicated aerospace and defence industry operations.
“I gave Cincom an hour of hell at that meeting, but they demonstrated real knowledge of this type of business,” said Quinlan. “They made it clear their product would work for us.”
Business Systems Manager Malcolm Boadle coordinated thee design and technical implementation. For him, key to a functional and widely used ERP was ownership throughout the selection and implementation process. “Our managers knew they had a vested interest in making sure the system met their requirements. They were tasked with satisfying themselves that the system would help execute their particular duties and effectively run our business.”
Vegvari said vendors assessed included SAP and Oracle. “We chose Cincom because of its price and the package of capabilities it offered, and the fact that it best suited our business requirements. It was also reassuring to know that other businesses in similar areas to us were using Cincom.”
Results
A team of Cincom and TUS personnel completed the initial installation of the ERP suite of finance, manufacturing and engineering applications in a ‘big bang’ approach, terminating the outsourcing arrangement as soon as possible. “The implementation was rapid for an operation of our size – about 8-9 months, including training,” Vegvari said. “We had a tight deadline and Cincom came to the party and met it. The Cincom people were excellent; they were quick, professional, answered our questions and were obviously well-trained.”
“We had a tight deadline and Cincom came to the party and met it. The Cincom people were excellent; they were quick, professional, answered our questions and were obviously well-trained.”
As for the results: “We have improved our decision-making and reporting capabilities. said Quinlan. “For instance, we recently had a corporate restructure. Getting the necessary in-depth reports from the service provider would have been difficult and time-consuming; the CONTROL system enabled us to access the required data without needing additional resources.”
CONTROL is a step forward, Vegvari agreed. “It’s a full ERP system, covering manufacturing, projects, purchasing, automatic ordering, as well as accounts payable, accounts receivable and general ledger. It has consistent Windows-based screens that we all feel familiar with, which has resulted in more efficient training. CONTROL: Financials is very logical. It works very well for accountants, so out financial operations are now streamlined.”
Easy access to data means the required reports are rapidly and automatically produced. “That means we can spend more time analysing the results.”
Boadle cites greatly improved interdepartmental relations as a significant benefit of implementing Cincom CONTROL, saying the selection process opened strong lines of communications that still exist between personnel in different departments.
“All up it was an exemplary result in terms of achieving our goals and value for money,” said Quinlan.
“Cincom has provided a more cost-effective solution that gives us better integration of information, increased flexibility and more streamlined financial processing. The improved access to information enhances our decision-making capabilities.”
FURTHER READING
About This Vendor
More Case Studies

Cincom powers organic growth for fruit and vegetable supplier
Software vendor prioritises T&F All States’ connection to freshness…