Published on the 09/08/2018 | Written by Jonathan Cotton
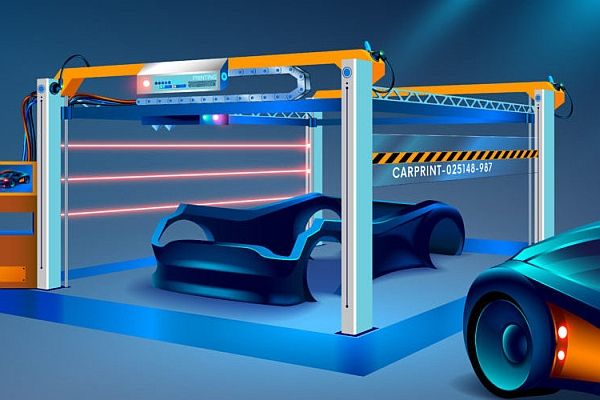
3D printing is here, it’s awesome, and it’s going to revolutionise manufacturing…
Printer speeds are increasing, new printable materials are hitting the market, and executives are looking for new ways to embed it in their manufacturing processes.
3D printing (AKA ‘3DP’ or ‘additive manufacturing’) is no longer the domain of the hobbyist. Rather, in 2018, industrial-scale 3D printing is laying down some serious growth.
How big is the market going to get? Predictions vary.
“Focus has shifted away from the consumer and rapid prototyping, towards the digitisation of workflows and the manufacture of production quality final products.”
Back in 2016 EY forecast that by 2028 the global market for 3D printing equipment, materials, software and services would hit the US$22 billion mark. According to 3D Printing Market: Global Industry Analysis, Size, Share, Growth, Trends and Forecast 2017 – 2025, the global 3D printing market will have already reached US$32.3 billion by 2025.
Either way, its big and it means that optimised supply chains, efficiency gains, quicker turnarounds and lower costs are on the horizon. And at that prospect global players – most notably global megaliths GE and Siemens – are getting excited. GE has recently announced its plans to build a US$1 billion 3D-printing business by 2020. Siemens has already opened a 3DP facility in Sweden and is currently partnering with universities to improve its additive manufacturing chops.
From a technical standpoint, the market is currently split between methods of 3D manufacture: Fused Deposition Modeling (the most widely used form of 3D printing at the consumer level), Stereolithography (the first 3D printing technology, developed in the ‘80s) and Selective Laser Sintering, the most common additive manufacturing technology for industrial applications.
“Focus has now shifted away from the consumer and rapid prototyping, and towards the digitisation of workflows and the manufacture of production quality final products,” says Bryony Core, author of IDTechEx’s 3D Printing 2018-2028: Technology and Market Analysis.
“Several industries are now seriously analysing the benefits and competitive edge that 3D printing can lend their operations, and the most eagerly anticipated technological innovations are catering to these professional users.”
So how does it play out on the shop floor?
Aerospace is big on 3DP manufacturing, thanks in part to the low-volume, high-value production typical of this sector, as 3D printing can produce products that are faster and lighter (better weight to thrust ratio) and less wasteful (more fuel efficient), all while being cheaper than traditional production methods. GE’s Leap aircraft engine, for example, includes some of the first FAA-approved 3D-printed components – nineteen 3D-printed fuel nozzles – which are projected to last five times longer than traditionally made components.
The medical field is another industry excited about the potential, with the growing use of 3DP in the customisation of prosthetics and dentistry, as well as the growth of bio-printing, with scientists printing human-sized bones, cartilage and muscle.
Recently doctors at the NYU School of Medicine created 3D printed ceramic “scaffolding” that guides the regeneration of bone within the body then dissolves harmlessly into the body once it’s done its job.
Even the food industry gets a look in with one pioneering German nursing home adopting 3DP to create Smoothfoods – an apparently palatable concoction of mashed peas, carrot and broccoli – perfect for elderly residents who have difficulties chewing. Over 1,000 such facilities in Germany have now adopted the process and the EU has invested nearly US$3.3 million in the project.