Published on the 25/10/2023 | Written by Heather Wright
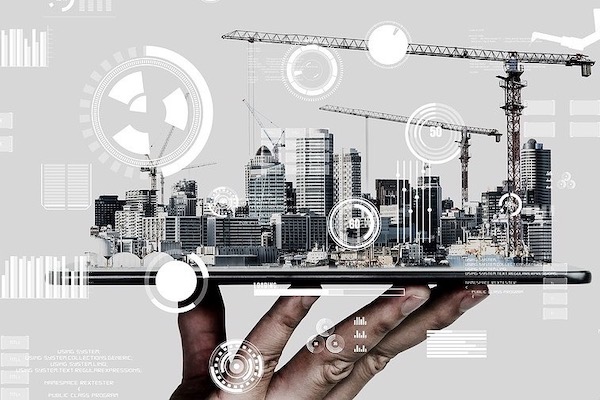
Catch-20 hits sector…
Construction technology – sometimes somewhat unfortunately dubbed ‘con-tech’ – may be evolving and transforming the sector, but digital shortages are continuing to hamper the industry.
A new report from the University of Melbourne, in partnership with Autodesk, shows that shortage is impacting quality and safety protocols in the Australian construction sector, with a lack of clarity and audit trail for decision-making processes, and difficulty in capturing ‘as built’ information among the top issues reported by 50 percent or more of respondents.
“61 percent believe using new technology is one of the top sources of revenue growth,”
According to the report, Construction Quality and Safety 2023, difficulty accessing data, managing and maintaining data and lack of due diligence process were also key issues.
Construction, just like other industries, has been undergoing digital transformation. Challenges such as the labour shortages, supply shortages and surging costs for building materials and demand for increased efficiency and sustainability. Increasing interest rates, meanwhile, have dampened down future work, reducing the pipeline in the short term at least.
Productivity rates for the sector are seeing little upward movement – in two decades they’ve increased just one percent per annum according to a report earlier this year.
With that in mind, the sector is increasingly looking to technology.
A report earlier this year by Deloitte Access Economics on the state of digital adoption in construction, found that 61 percent of respondents believed using new technology was one of the top sources of revenue growth, while 48 percent saw new technologies improving internal business processes, such as e-invoicing, as a source of growth for their business. Those using technology cited benefits of increased productivity, improved customer experience and increased staff safety, suggesting that effectively using technology could address some of the biggest issues the sector faces.
The report, commissioned by Autodesk and looking at companies in Australia, Singapore and Japan, found that 40 percent of businesses surveyed (mainly the larger and longer established businesses_ were using Building Information Modelling (BIM), with 39 percent using cloud software and 33 percent using data analytics.
It also found the use of each additional technology was associated with a 0.58 percentage point increase in expected revenue each year.
But it too, highlighted concerns about the issue of lack of digital skills among staff hampering adoption, along with uncertainty about the required skills and a lack of budget allocated for increased technology adoption.
It’s a similar story in New Zealand where a Building Innovation Partnership paper notes that construction ‘sits markedly lower in the rankings of all sectors when it comes to developing and using digital technologies, although some technologies such as BIM are starting to penetrate parts of the sector’.
“Some commentators believe the slow uptake of digital technologies provides opportunities for disruptive innovation of the sector,” Lindsay Crossen, BIP overview panel chair says, noting that while that may be true, there are still many hurdles to digitalising construction.
BIM has been touted as the foundation of digital transformation for the sector, enabling recording and managing of information about a construction project throughout its entire life cycle. Providing intelligent 3D modelling, it also enables streamlining of workflows and early analysis to save time and money and lead to fewer variations during construction, and can ensure all parties involved are across all changes – minimising disputes.
Driving uptake of BIM in New Zealand is one focus of the second Construction Industry Transformation Plan. The plan has a strong focus on leveraging digital technology, including initiatives to increase uptake of digital engineering (of which BIM is one form) and the Construction Digital Boost 2.0 program to help SMEs grow their digital capabilities, such as managing finances, placing orders, and submitting and receiving invoices, using digital tools.
Building on BIM, digital twin technologies integrate real-time data from a build set with its exact 3D virtual replica, enabling the sector to more effectively monitor the performance of a build and test ‘what if’ scenarios including impact of design changes or construction sequencing.
Data security and ownership issues, lack of common data standards and tools and diversity in source systems are among the challenges to digital twins according to New Zealand’s Ministry of Business, Innovation and Employment (MBIE).
Nonetheless, as part of the 2021 Australian Infrastructure Plan, Infrastructure Australia set a goal of ensuring all federally funded infrastructure projects incorporate a digital twin within the next 10-15 years and the Australia and New Zealand Land Information Council has developed principles for spatially enabled digital twins of the built and natural environment in Australia.
Furthering the BIM action, this week the Korea Institute of Civil Engineering and Building Technology created a scan to BIM-based reverse engineering technology which it says eliminates errors and manual rework when transforming 3D scan data into BIM models, traditionally done manually or with expensive software.
The technology automatically segments objects from 3D point cloud data, extracts shape information and generates BIM objects, in a move KICT researchers say can lead to a 24-times improvement in productivity and a 110 percent increase in modelling information.
The use of mobile devices, cloud, drones and laser scanning is creating opportunities for quick and efficient capture, sharing and management of data, and enabling autonomous processing and analyses of large datasets in real time. That provides the ability to make better informed decisions on everything from site monitoring to production of ‘as built’ plans, and provides greater visibility for safety.
AI and big data analytics hold the potential to improve processes even further, mining useful information and improving intelligence.
MBIE’s 2022 Building and Construction Sector Trends report notes virtual reality, augmented reality and mixed reality as part of the growing digitisation movement in the sector, enabling clients to ‘experience’ designed spaces before they are built, manage sites remotely, monitor health and safety and enable collaborative working, training and quality control.
Wearables, including personal protective equipment with built-in sensors to track body movements and collect data such as heart rate, body temperature and blood pressure, and track the users location are also available to enhance worker safety.