Published on the 03/11/2013 | Written by Epicor Software Corporation
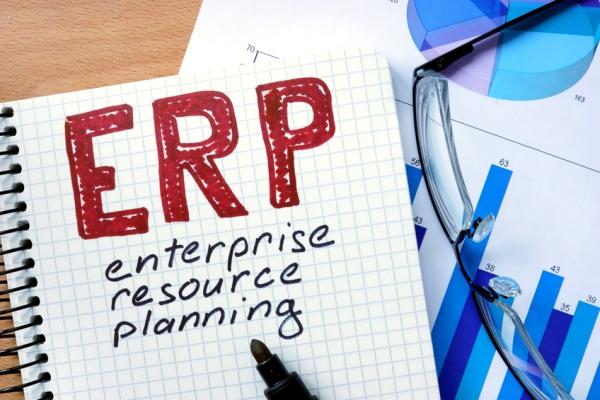
You might have several reasons for needing a new ERP system, but with so many options, how do you make the right choice? The experts at Epicor share their knowledge…
It’s no secret that selecting an ERP system can be a daunting task. If you’re wondering whether a generic or an industry-specific solution is the best fit, or how to start the ERP selection process, you’re not alone. The eight-step selection process Form an evaluation committee that includes top management, functional experts, and end-users from each department throughout your company. During the selection process, end each step with a consensus of all members to gain enterprise-wide acceptance of the final ERP system. Assess your existing business processes and the scale of your operation, so that you can determine what’s being done well. Identify gaps or key challenges that can be solved with the help of an ERP system. Develop selection criteria to evaluate available solutions. Criteria can include features like traceability, integrated EDI, recipe or formulation management and bar code capabilities, or integrated production scheduling; price; platform; and anything else that’s important to your business and industry. Group and rank criteria according to importance to your business and assign a score to each to make the evaluation easier. Arrange a 10-minute phone consultation with a sales representative and product expert from as many different ERP vendors as possible. This ‘discovery call’ will provide you with better insight about each vendor and their solution than if you were to rely solely on sales literature. Shortlist two to four ERP solutions that best meet your business needs. Your discovery calls will have helped you eliminate the solutions, which are poor fits. Arrange for each ERP vendor to deliver a live presentation and product demonstration. Prepare questions to address your most important requirements, needs and concerns. How each vendor responds will help you determine the best fit for your company. Check vendor references by visiting and consulting with companies that have implemented the ERP system. Ask if the system is working as expected, and what the company likes or dislikes. If there were issues, explore how the vendor resolved them. Generic and industry-specific ERP systems When an ERP application has been developed specifically for your industry it is better equipped to handle your manufacturing process with minimal or no customisation. This means faster, more affordable implementation and maintenance. Furthermore, an industry-specific ERP module typically offers deeper functionality for your specific business and operations needs than a generic ERP package. For example, an integrated, whiteboard-style production scheduling application allows the production planner to do his or her job within the ERP system, instead of using manual, offline spreadsheets. Generic ERP systems with vertical extensions Consider the industry expertise and experience of the partner that provides the front-end packages. Does the team understand your industry? Is there a strong user base? If not, who will be responsible for the cost of maintenance and development of the applications? Dealing with multiple software vendors can sometimes be a headache. When software issues arise, is it clear who will be responsible for resolving your issue? What happens if the vendors end their partnership? Weighing it all up Industry-specific solutions are implemented faster, and are less expensive to install and maintain. Although generic ERP system vendors may have software partners who offer front-end packages that target industry verticals, you should consider the issues of dealing with multiple vendors. Finally, by selecting a vendor that partner with you long term, and who understands the unique requirements of your industry will increase your chances of a successful project. Why, when, and how to invest wisely… The benefits of incorporating a data warehouse when upgrading your ERP… What to expect for the future of payables… Manual processes can lead to error-prone data analysis… What is a Finance Department and Manager Level KPI?…
To help you simplify the selection process, keep in mind these eight easy steps.
While most generic ERP solutions have modules to handle the non-manufacturing areas of your business, these systems often lack key functionality to handle manufacturing-specific process. You can customise a generic ERP application to fill the gaps, but this can be time consuming and costly to implement and maintain.
While generic ERP systems may have partners that provide front-end packages that target various industry verticals, consider how well the front-end package integrates with the generic ERP and your existing systems. Multiple systems require synchronisation and on-going maintenance.
Implementing a new ERP solution is a big task. Make sure you have the right people involved from your organisation, and spend some time developing relevant selection criteria to meet your business objectives. While you can choose between a generic or industry-specific ERP system for your business, an integrated ERP system specific to your industry will be better equipped to handle your manufacturing requirements than a generic ERP system.FURTHER READING
Financial reporting and analytics solutions
Whitepaper: Data warehouse automation and ERP
eBook: The new AP department
Whitepaper: Streamline your financial year-end close
KPIs and Metrics for Finance Departments in 2020